Sustainable Manufacturing Takes Root in the Heart of Texas
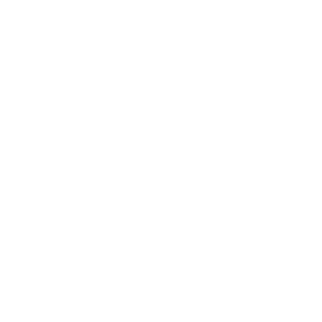
On 14 acres west of Austin, Texas, a home-grown manufacturing business is delivering on a sustainable vision. Rehme Steel Windows & Doors manufactures high-end, architectural steel doors and windows for some of the most discerning customers in the U.S. Company founder Peter Rehme, an Austin native, decided to build his factory in the Texas Hill Country because he’s fanatical about quality and wanted to stay close to the design and fabrication process. But building locally also helps deliver on the company’s mission to handcraft simply the best steel doors and windows on the market, and to do so with environmental sustainability in mind.
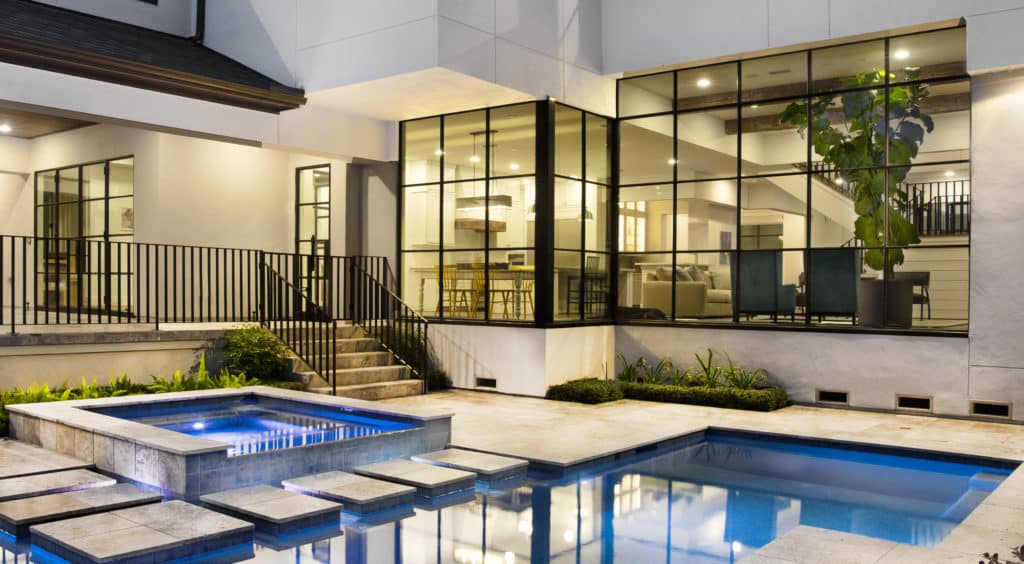
Sustainability has become a loaded word layered with multiple meanings of late. To some businesses, sustainability is all about environmentalism, and is core to the company vision. Outdoor apparel maker Patagonia includes sustainability in their mission to “Build the best product, cause no unnecessary harm, use business to inspire and implement solutions to the environmental crisis.”
To others, sustainability is part of a long-term strategy – having a sustainable vision today so you’ll be in business tomorrow. Sustainability incorporates socially responsible business practices, care for the environment and a business strategy that will stand the test of time.
Rehme Steel belongs in the second category. The company operates sustainably because it makes sense for the business, the employees, and for the environment.
Company founder Peter Rehme takes a lifecycle view of the production process – from the steel used to build their doors and windows to the energy powering the manufacturing process, to the scrap metal and other waste produced as part of operating a manufacturing business.
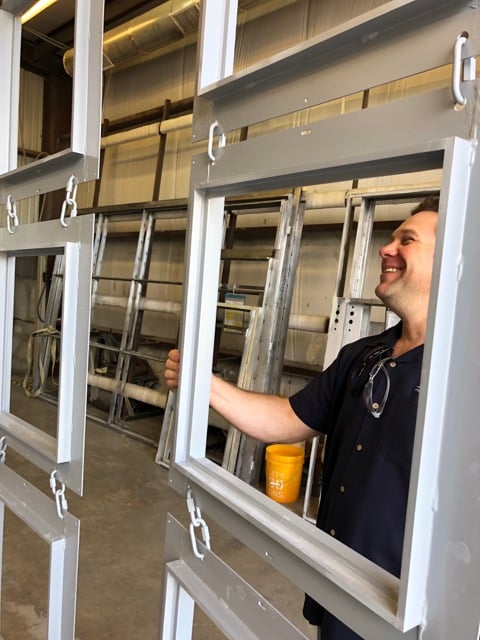
Rehme sources 100% American steel because he believes the quality is better, and he wants to support American jobs. But not having to ship steel from China to Texas also avoids the emission of thousands of pounds of CO2 from transportation fuels. Every bit of the sourced steel is recycled from scrap, making it one of the most sustainable raw materials in the building industry.
Recycled steel is just the tip of the iceberg, sustainably speaking. Rehme’s team is vigilant about recycling everything from cardboard waste to soda cans to leftover pieces of scrap — carbon steel, stainless steel, aluminum and copper alloys. And if they’re concerned about the factory’s energy use all they have to do is look up: All five buildings on site are covered in solar panels.
Building Better Doors and Windows, Powered by Solar
Welding machines, sanders, grinders, saws and drilling machines are just some of the tools employed daily to craft Rehme’s products. Some of the buildings operate with the doors open whenever possible, helping with circulation and daylighting, but humidity control is crucial, meaning lots of fans are needed to circulate air. All of this energy was a drain on company resources, as well as the environment.
In 2017, Rehme installed a solar power system that now offsets 105 percent of the factory’s electricity use. (The extra energy is credited to their utility bill for times when solar isn’t meeting the full demand.) Better yet, it’s estimated that over its 25-year lifetime the system will offset the equivalent carbon emissions of driving 210,294 miles in a fossil-fueled passenger car.
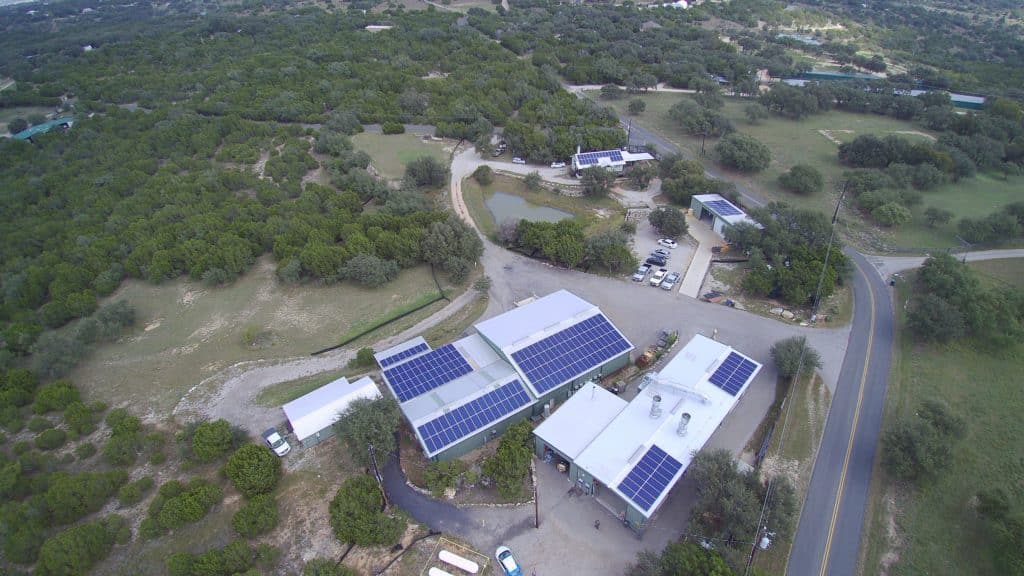
Austin’s Freedom Solar designed the system, optimizing the size and layout to match each building’s energy load as closely as possible. The fabrication facility, where the welding and most of the assembly takes place, was the biggest energy consumer with the largest roof, so three-fourths of the system’s 240 panels were installed on its roof.
Why Sustainable Manufacturing Makes Sense, Even in Texas
When you ask Peter Rehme why he believes in running his operations sustainably, he will wax poetic, but only a bit.
“Being environmentally conscious is part of my DNA but as a business you have to do more. We have 40 employees and that creates a lot of waste. So we do what we can. It’s impossible for me not to.”
“I do believe there are greener ways to run this earth than burning fossil fuels,” he emphasizes. “But you can’t run a business making green decisions only. When a decision is green and also a good business decision, it’s a no brainer.”
With solar costs plummeting over the last several years, going solar was a good business decision. The system will pay for itself in less than four years. Over the next 25 years the system is expected to return nearly $350,000 to the company’s bottom line in electricity savings.
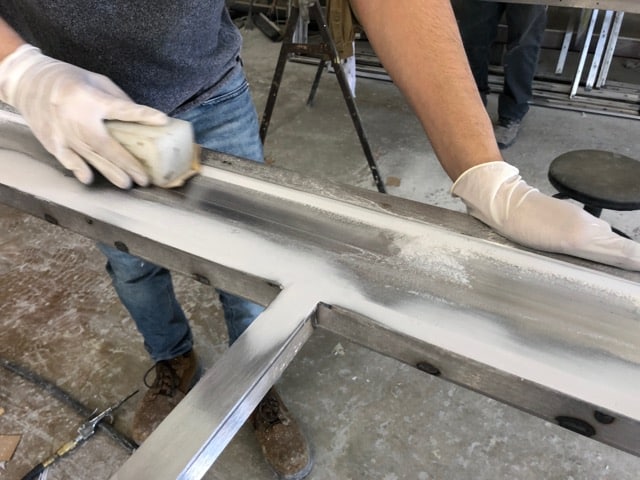
Employees are on the front lines of Rehme’s sustainability strategy and became more aware of their carbon footprint in part through the energy monitoring system installed with the solar. Rehme now has a bird’s eye view of the facility’s energy consumption, and can zero in on specific areas that are overconsuming.
“Everyone really bought in to reducing energy use once the solar was installed,” Rehme says. “It changed the culture.”
For most businesses, sustainability is a journey, not a destination. By being open to the possibilities of sustainable manufacturing, Rehme took a giant step forward in his company’s sustainability journey. And already it’s paying dividends — for his products, his employees, and for the Texas Hill Country.
Stay in touch
Get information just like this in your inbox.
Unsubscribe at any time
About the Author
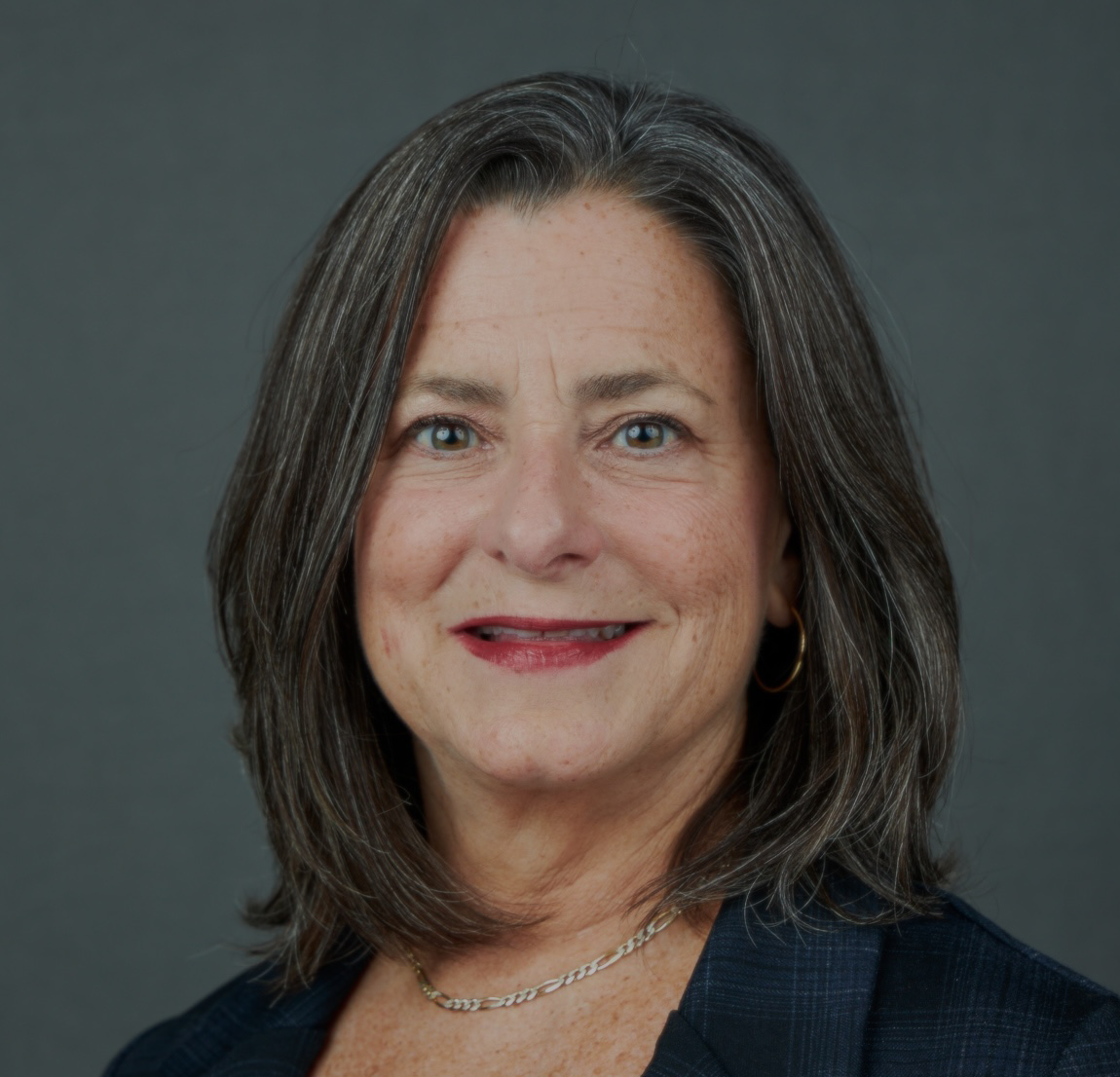
Nancy Edwards
Founder/Managing Partner
Nancy Edwards is founder and managing partner of Clean Power Marketing.
Ready to Power Up Your Marketing?
At CPM, we work with the game changers, the innovators, the leaders tackling the planet’s most urgent environmental challenges. If you’re one of them, we’d love to collaborate with you.